Current projects
Microstructural integration for cascade catalysis
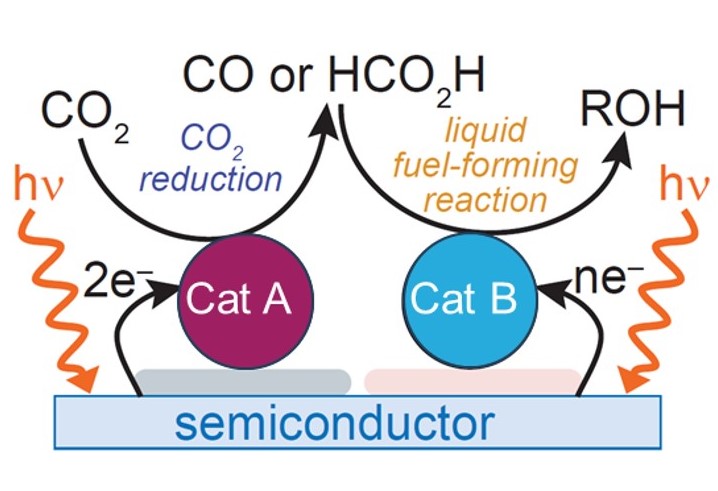
The Lopez Lab is part of the Center for Hybrid Approaches in Solar Energy to Liquid Fuels (CHASE)
which is a Department of Energy Fuels from Sunlight Hub. CHASE’s mission is to develop molecule/material (hybrid) photoelectrodes for cooperative sunlight-driven generation of liquid fuels from feedstocks found in air: CO2 and H2O. The Center is pursuing these goals through three interconnected Thrust areas: Thrust I: Catalyst-Semiconductor Interfaces; Thrust C: Cascades Catalysis, and Thrust H: Catalytic Hybrid Photoelectrodes. Our research lab’s involvement in CHASE has included development of Nitride materials (closed project) and currently the the immobilization of molecular cascade catalysts on semiconductor surfaces.
This is a promising methodology for the development of photo-electrodes that can efficiently and selectively convert solar energy to commodity fuels. Molecular catalysts are attractive targets because of their product selectivity, but current state-of-the-art catalysts can generally only produce 2-electron products. A catalytic cascaded reaction is a possible pathway to produce useful C2 products, such as ethanol, and beyond. Here, two or more catalysts work in tandem, with a primary catalyst reducing CO2 by two electrons, and a secondary catalyst using this product for a reaction that further upgrades this species. To achieve a cascade with immobilized molecular catalysts, two different catalysts must be attached in two different places on an electrode surface, requiring precise control of the chemistry at the electrode surface and orthogonal attachment strategies. The relative placement and spatial distribution of the catalyst plays a crucial role in their cooperative performance. The goal of this project is to develop 2D surface patterning and 3D structural scaffolding to support orthogonal integration strategies and to address the challenges catalyst co-compatibility and intermediate hand-off for cooperative catalysis.
Additive Manufacturing of High Performance Amorphous Polymers
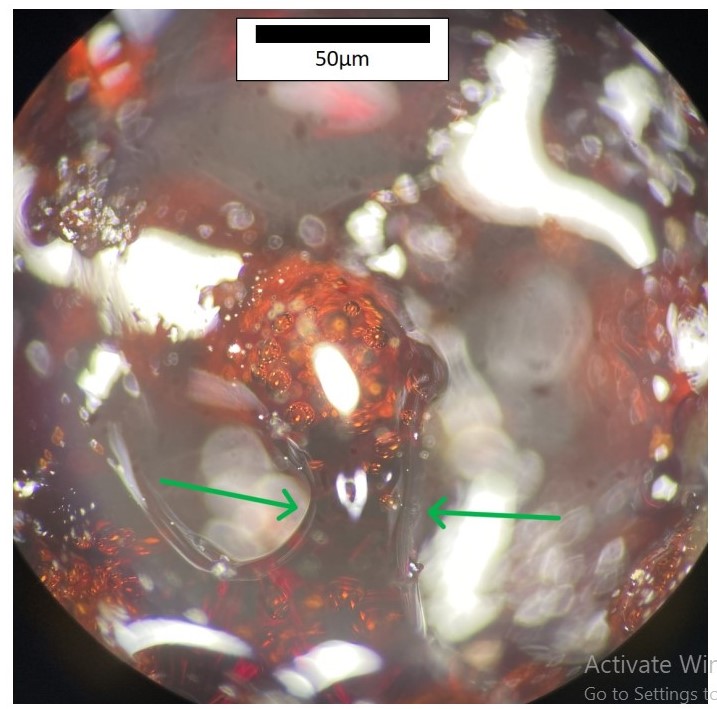
Additive manufacturing (AM), commonly referred to as 3D printing, is a widely popular technique for producing a large variety of complex parts without requiring an equally large variety of specialized tooling. It provides a unique opportunity to transport a compact volume of light-weight materials into space where the required equipment can be rapidly manufactured. While AM techniques like selective laser sintering (SLS) and filament deposition modelling (FDM) are well established, many applications are not yet realizable due to the lack of printable materials capable of withstanding the large loads and high temperatures sustained in many developing space technologies. Many think that the difficulties encountered when printing with high performance polymers are too challenging to overcome and deem these polymers impossible to utilize in AM. Our collaborator Prof. Theo Dingemans already shown that a modified chemistry will lead to printable high performance materials with glass transition temperatures higher than their commercial counterparts. Further refinement remains to ensure that the printed parts maintain exceptional integrity under various stresses. Since the results are highly sensitive to the print settings, a study of the coalescence characteristics during the SLS process is necessary to optimize the operating parameter space. Material testing will then be performed and a physics-based model will be constructed to verify results and check our understanding of the underlying physics.